Engineering Leadership Series - Andrew Goldman
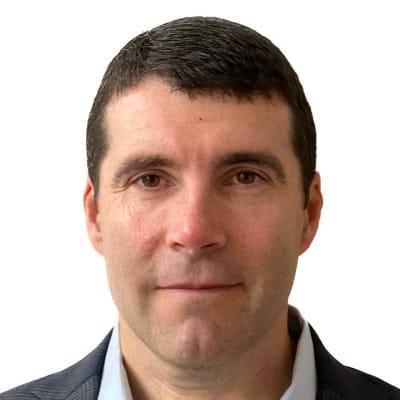

Today we have another outstanding guest in the Engineering Leadership Interview Series. Andrew Goldman, the Head of Hardware Engineering at Formlabs joins us to share his story.
We discuss the challenges developing physical hardware vs software, how engineers can effectively apply business principals to see the bigger picture, how Formlabs is changing the game in 3D printing, and what it takes to effectively lead a team of 100 + people.
Andrew brings a wealth of knowledge and experience to the table and the insights he shares are invaluable to both established and aspiring leaders.
Enjoy the interview and give Andrew a follow.
More Information
Andrew's LinkedIn
Formlabs
Formlabs Careers
The Interview
DoneStreet
Let’s jump right in. Can you tell us your story? How did you discover your interest in engineering? Was it from a young age?
Andrew
Yes, I went to school for physics. I was really intensely curious. Always have been about how everything in the world works. After I got out of school, I quickly realized that if I want to increase my odds of bringing useful things to the world, I needed to pivot to engineering. So, after college, I used my optics background from physics and started making hardware products.
DoneStreet
Yeah, you've had a pretty interesting career. As you mentioned, you've been a physicist, an optical engineer, and now you lead a team of roughly 100 people. What lessons did you learn along the way, or early on, that you still carry with yourself today that you think contributed to that success?
Andrew
I think that the biggest lesson I learned is that when you're talking about industry, you're not doing engineering for the sake of engineering. There's always some business purpose as to why you're doing it. And I think if you can start to connect your technical work to the business goals, you become a much more powerful engineer. Basically you go from being an engineer that'll just blindly do the task that your manager asks you to do, to now questioning the requirements and assumptions and cutting through all the noise and get from A to B as fast as you can. And sometimes if you're creative and you really understand what the business is trying to do, you'll come up with better ideas than your manager has.
That's a lesson I learned really early on.
DoneStreet
I'm curious, have you ever noticed a pattern between people who were trained very heavily in academia, maybe like the master's or PhD route, and people who might have gone into industry earlier. Have you noticed a pattern between if they're able to grasp that concept sooner or later?
Andrew
Yeah, absolutely. It's a great insight. There are certainly some PhDs who can pivot to industry easily, but I found that it is not natural for most of them. I have had much better luck, in general, just hiring people who stopped with a bachelor's degree. Even though they learn less things in school I guess, they really get to be more productive engineers faster than PhDs. As I said, there's exceptions, but it's pretty rare. I would say there's not a ton of PhDs I've hired, even when I've been really hopeful, that have easily made that leap.
DoneStreet
Okay, interesting. Yeah, that's kind of what my guess would have been. It's interesting to hear that confirmation though.
You've been with Formlabs for roughly nine years now. How did you originally get hired there and join the team?
Andrew
I joined Formlabs when they were really small. They were basically still a startup and not guaranteed to succeed. They had not hired an experienced engineering manager at that point. So I was the first engineering manager who ever worked here. At the time, they weren't sure what they were even looking for in an engineering manager. And I certainly wasn't sure that it'd be a good fit. But over a few conversations, we were both kind of intrigued enough to give it a try. And nine years later, here I am, so it worked out.
DoneStreet
That’s pretty awesome because obviously the company's a lot more established now and in hindsight, it might might not have seemed so obvious. From my understanding, Formlabs is a company that specializes in 3D printing technology and digital fabrication. So you're really looking to help industries like manufacturing, automotive, space, and potentially healthcare. What problems are you solving that the market was missing?
Andrew
Yeah, you know, all the above. We have a lot of different verticals. I think the best way to think about this is that when we entered the market, there were two categories of 3D printing. There was the industrial 3D printers that made really nice parts, but they were hundreds of thousands of dollars and the size of a small conference room. They were really difficult to use. And then there were these hobbyist printers. And the hobbyist printers were affordable, but low reliability, low throughput, bad dimensional accuracy, and bad material properties. So the only people really using 3D printing were hobbyists if they just wanted to make a trinket, or really large companies who could afford to invest in it.
We thought, hey, 3D printing is a tool that can be really useful in the world, but we need to make something that's both affordable and useful. And that's really what we did. We’ve basically developed a few full ecosystems of 3D printers at this point. From the software to the hardware to the materials to the post processing, we designed all of that and make it all work together. Our printers range from roughly $2,000 to $20,000. So it's affordable to pretty much any business. And they're also useful. They’re high throughput and they're industry leading reliability. They're really easy to use and anyone can be printing within 15 minutes of taking the printer out of the box.
They produce really great part quality when it comes to surface finish and dimensional accuracy, and we provide a large whole library of really useful engineering materials that can be applied to many markets.
DoneStreet
That’s very interesting. How do you see AI playing in there? I've seen some videos of people designing things in AutoCAD through text to CAD. Is that something that you're building on top of? The ability for people to really easily design things and then print them. How does it work from when a customer gets one of your printers, do you provide prefabricated designs for them or how does the design process work?
Andrew
At this point anyway, we’re not really trying to do the CAD part of it. So the flow would be something like users have a CAD file, whether they generated that themselves or they got it from somewhere else. There are plenty of places to get one, and then they can bring it into our ecosystem and then you can get a physical part out. So I think the AI, some kind of voice to CAD would be good for us. If there can be more CAD users in the world, then that's better for us. So I'm all for it. But we're letting other people do that right now. We have so much more that we can do with the tools that we're not at the point where we need to worry about that end of it yet.
DoneStreet
What else is your team building today that you're excited about? Are there any new or exciting products that you guys are building?
Andrew
There is, but I can't give away any state secrets. So let me try and answer it slightly differently. I’ll tell you why it’s fun to develop 3D printers. It’s fun because they're really complex and multidisciplinary. There’s optical systems, there's thermal systems, there's motion systems, there's sensors, there's embedded firmware, and there's software that lives in your PC. There's a bunch of algorithms you've got to get right. And you’ve got to get that all together and make it work to have a 3D printer. There’s also material science, I forgot about that big one. What I found working here is that it's pretty easy to make a 3D printer that can print something, but it's really hard to make a 3D printer that can print any geometry that our customers can dream up. And that's what we're trying to do. Allow them to print that item reliably over and over again across tens of thousands of printers and get the same part every time. That's a huge challenge, and it makes it really fun to work on these things.
DoneStreet
It seems like a lot of the printers are in the corporate space, we talked about some of the verticals earlier like health care or automotive. Are you seeing more progress in the individual homes using a 3D printer to print things for their daily life?
Andrew
Formlabs is about 13 years old so we're just getting started. The approach we are taking is that we are trying to design tools for businesses. Now, that doesn't mean hobbyists can't get them. But the philosophy here is that businesses who are going to buy this thing and use it to make money are going to be a lot more demanding than the hobbyists. So, if we can get the performance that is needed for businesses, then over time, we will keep costing it down and maintaining the performance. Naturally hobbyists will buy it. I think our desktop printer, the Form 4 that just came out is around $4,500. There's definitely hobbyists that buy it. We're just not trying to market to them or intentionally serve that industry.
We're trying to make the right tool and make it amazing. Then we will drive the cost down over time so that hobbyists can also buy it and use it in their house.
DoneStreet
Yeah, that makes a lot of sense. Unsure if this is a complicated question, in the health care space, typically medical products have to go through all kinds of regulatory approvals, which might takes years. If 3D printers are printing some kind of medical product that might be used in surgeries or actually go into the patient. How does this line up with what we think of as the historical regulatory process? I would image there could be some variance in what the surgeon or doctor is printing. Can they just print new things and use them immediately in the hospital?
Andrew
For the printer themselves, we don't need to make those ISO 13485 or anything like that. However, the materials used in the process are what you need to get through the regulatory. We have bio compatible materials and those have gone through the full certification process. The process is that you print the part and then you need to wash it and post cure it. We do all the work to certify that, and then we tell the customer, “If you want it to be certified, this is what you do. You need to post process it for X amount of minutes at this temperature and this optical power.”, and we give them all the equipment to do that as well.
But the equipment that we sell that never touches the patient, we don't actually have to certify those.
DoneStreet
Gotcha, that makes sense. When you think about the challenges between hardware engineering and software engineering, what do you think are the hardest challenges and aspects that really differentiate them? Is it the fact that it's physical atoms and putting things together, or are there other challenges that might be often overlooked?
Andrew
Yeah, software guys have it easy. I have software embedded firmware people working for me as well. And I've led software teams before and so if I'm a software engineer, I do all the design work and then I can press enter and see immediately if it is going to function the way that I want it to function. And if it doesn't, I can immediately start figuring out where the bugs are and start iterating on those really quickly and get to a place where it's good. You can use a little less rigor there. For hardware, you have to do that same amount of design work, but then you need to fabricate parts. That's expensive and time consuming.
What it does is it makes your iteration cycle slower. You get less of those. And then once you get to the point where you iterate a few times, you get your parts to a point where they're functioning the way you want to. In the real world, physical parts wear out like motors, lasers, etc. But now you have to do a whole bunch of reliability testing, so the cycle is just way longer. And that means that you need to have a sharper focus. You need to be better at things like understanding the true requirements up front, having a better design review process, and estimating what's going to work and what's not going to work because you have fewer tries to get it right.
DoneStreet
For sure. It seems like it’s much more cost prohibitive versus software. With software, you just ship it and then you find out if it works. With hardware, if you invest a lot of resources in something and don't plan properly, then your risk a lot of overhead loss and sunk costs.
Andrew
Right. I think in 3D printing, we're part of the solution to this problem. We use our 3D printers all the time to develop our product, and it's good, but it's nowhere near the pace that software can go.
DoneStreet
When you say you use your own product to develop your products, are you printing parts for the 3D printers themselves?
Andrew
Oh, yeah, 100%.
DoneStreet
That's awesome.
Andrew
For prototyping all the time. Even if you get one of our products and look closely, there's always half a dozen to a dozen 3D printed parts that we actually ship on our products at this point.
DoneStreet
Oh, that's very cool.
Andrew
We put our money where our mouth is.
DoneStreet
Do you foresee any limitations with 3D printing? Or is the sky really the limit? Are they going to be able to 3D print entire cities and houses? Or do you think there are complications that might prevent that from being possible?
Andrew
No limitation. Even today, people print plastic, metal, ceramics, PC boards, cement, human organs, and that's just today. I think in reality as an engineer though, I would never use it for some products. I'm really passionate about using the most efficient process to fabricate things. And I think 3D printing will be more of a complementary technology to other fabrication processes. Not because I can't do it, but just because it doesn't make sense. For example, if I have a simple plastic part and I want to make a building of them, I can 3D print them, but I shouldn't 3D print them. I should use injection molding. It's going to be way cheaper and more efficient and use less energy, etc.
I think 3D printing has evolved a huge amount compared to injection molding and machining. I think they've figured out all the things they're going to do and 3D printing is going to take a lot of that. But I don't think it'll replace every manufacturing technique. It wouldn't make sense.
DoneStreet
So if it's a lot more complex of an item, it would make more sense to 3D print it.
Andrew
Yeah. If it has internal geometries and all that, you can't inject a mold and you can't machine it. One of our huge high-volume applications is dental. Everybody's teeth are different. So, even though they're printing tons of implants, or producing them, you can machine them, or you could injection mold them, but every single one's different. So, 3D printing is perfect for something like that.
DoneStreet
Right, that makes sense. Shifting gears a little bit here, you work as a mentor to many startups and you also serve as a chairman of the board of the directors of Boston Materials. I'm curious, how did you get involved with that company, and can you tell us a little bit about your role there and what that company is working on specifically when it comes to energy management and transfer?
Andrew
Yep, sure. I have a lot of experience at this point and if I don't share it with anyone, it's going to rattle around in my head. Not very useful. So, I started mentoring startup founders about six or seven years ago, maybe longer than that at this point, because I've been through a lot and I like sharing my experiences and helping people. That’s how I met Boston Materials. The founders were two kids out of school or just about to finish. They did a capstone project and thought it could be a cool technology to put out in the world. One of my former business professors hooked me up with them and I started mentoring them, including helping them navigate the strange and cruel world of venture funding.
Once they got some funding and they needed a board of directors, they were nice enough to invite me to join. It's been a fun learning experience. I’m grateful for that.
They make Z aligned carbon fiber. One of the attributes of carbon fiber is that in the direction of the fiber, it has amazing energy transfer properties. Whether it be electrical, thermal, or mechanical, it's better than most things in the world. So as an example, what we're focused on today is thermal interface materials. You wouldn't think AI and carbon fiber have anything to do with each other, but they do. And to power AI, you need physical semiconductor chips.
As the circuits in those chips get denser and the chips themselves get bigger; they start generating a ton of heat. So, you’ve got to get the heat out of the chips to be able to utilize them well. Boston Materials has developed this unique thermal interface product that's like a mixture of carbon fiber and liquid metal. And it has better thermal conductivity than anything else we've seen. Right now, they are working with all the big AI companies and working on getting their product qualified. There's a lot of other interesting applications like hydrogen fuel cells, hypersonics, etc.
I've always found that if there's a technology wave in the world and you can do something to propagate it, especially if you're a startup and you're not profitable yet, you’d want to put the other things aside and try and surf that wave as far as you can. So, that's our focus right now and I'm excited to see where it goes.
DoneStreet
That's very cool. And it sounds like some big brained people are working at that company to develop that.
Andrew
A great example, one of the founders stopped his PhD to do this. And that's a good example of someone who would rather produce something for the world than stick in academia.
DoneStreet
Yeah for sure, theoretical vs actual.
Andrew
Yeah, don't get me wrong, right? If you want to do theoretical stuff and work on the cutting-edge technology of what's next, that's awesome. It's just not how I'm wired. I want to make things get out there. That's what drives me when I work.
DoneStreet
Yeah, definitely. Your passion is evident. How do you balance so many commitments and ensure that you're effective at providing value to each of them
Andrew
That's a good question. It took some experience to do it. I’ve found that you can use a simple formula no matter how big your scope gets. This formula identifies what the biggest problems there are, whether it's within a company, a team, or multiple companies. Identify the people who might be able to help solve those problems, coach them up and point them in the right direction. And if any of those big problems are left, handle them yourself. That will work if you have a team of five people, or if you are trying to help hundreds of people over multiple companies.
So, I try to keep it simple and just use the same technique, whether it's within or outside Formlabs. It's just one big thing that needs to happen.
DoneStreet
Yeah, that's some great insight. It sounds like putting capable people in place and helping them get to the spot where they can solve problems themselves. Then you step in when absolutely necessary.
Andrew
Yes.
DoneStreet
Leading at such a large team, how do you generally approach leadership? What do you think makes somebody a good engineering leader? Are there certain things you try to do more or certain things you try to avoid?
Andrew
I think the good engineering leaders are the people who have a combination of technical acumen, product sense, program management skills, and people management skills. You can't just have one. You need all four of those. When you put into practice, the thing I try to avoid is micromanaging people. My most important job is hiring the right people and building our team and helping them grow. And if I find myself micromanaging someone, that means that I've done a bad job either hiring the right person or helping them grow. And I need to go and address that root cause and not just stubbornly put my head down and continue to micromanage someone.
I think the biggest thing I try to do is not micromanage.
DoneStreet
And how are you typically hiring or how are you thinking about building strong teams through hiring?
Andrew
I have two important things that I do. One is that I always prioritize potential for growth over experience or immediate experience. For example, if engineer A has some experience that can help me immediately, and then engineer B doesn’t have that experience yet, but I think in a year they will be twice as productive as engineer A, I'm going to hire engineer B every single time. I think that's way more important than the immediate experience. The second thing is that humans are bad at absolute judgment – telling if something is good or bad. The same thing is true when you interview, right? It's hard.
You're trying to figure out in 45 minutes if you want to hire someone for your company that might work there the next five years. What humans are good at is relative judgments. Comparing A to B. I try to use that when hiring. So, if I have someone that I think I might want to hire, I look at the function that they would go into, mechanical engineering or electrical engineering. Do I project them to be in the top half of my team or the bottom half of my team? And I just use a simple math, if they're in the top half, the overall performance of my team goes up, and if in the bottom half, then it would go down.
There’s one exception here, I love hiring high potential engineers right out of school. And in that case, I won't necessarily hold them to the top half of the team because it might just not be practical. But I'm not trying to hire them on the bottom of my team. I need to think that in a year or two they will be at least in the top three quarters of my team and still have growth potential.
DoneStreet
For sure. Those are great, simple and effective heuristics to speed up the process and systematize it.
Andrew
Yeah. I've seen a lot of people fail in organizations. Especially in an interview panel, if everybody says yes and you hire them and they don't do that extra step of asking “Are they better than the people we have already?
DoneStreet
I have not heard anyone mention that before. Definitely a valuable insight.
One of the things you mentioned earlier in our conversation was that you like having conversations with other leaders about what you do with generally productive people who aren't growing fast enough. It’s an interesting topic and I'd love to dig a little bit deeper there. What exactly do you mean by that and how do you generally handle that?
Andrew
Yeah, I think sometimes you hire someone, and they have an initial burst of growth, but then they plateau. They get to this place where they're not a net negative, however, you find yourself hiring a whole bunch of other people who are growing faster than them. Those situations are hard because they are doing things that are useful for the company. But on the other hand, you can hire people who are more productive than them. So, what do you do? You don't want to just fire people like that.
So, how I handle it today, and I'm not sure I handle it the perfect way, I have an honest and direct conversation about it. Just call them out and say “Here's what I see. You started to grow, and then you've plateaued over the last couple years”. I’ve found that sometimes it's just complacency and it's not a good fit for the company that they’re at. Or, what’s going on in the company has changed and it no longer aligns with them. And I think you just need to work together and be mature about it and try to figure out what the root cause is and resolve the situation.
Sometimes they just need a kick in the butt, and sometimes you have to align that they’re going to be better off somewhere else. That’s not in a cruel way. It's that you're not helping someone by keeping them at your company if you see no growth for them over the next several years.
DoneStreet
Definitely. It’s a tough topic. Have you found that people respond well when you have those conversations? Does it push them towards one of those two paths where they either get their act in gear or they understand that it's not the best fit for them?
Andrew
I do. And that's the thing that’s unnatural. In your everyday life you're not having weird and awkward feedback conversations with your friends and saying, “I think you could drive a little better or whatever”. It is one of these things that only happens at work. But, I've found over time that if you take the filter away and have an honest and direct conversation, it's way more helpful and productive for the person than if you just dance around the issue.
DoneStreet
For sure. Makes sense.
We noticed that you've been granted maybe 15+ patents over the past decade or two which is amazing. Do you have any insight for someone who might be thinking about applying for their first patents and has not really gone through that whole process yet?
Andrew
Yeah, I think the best insight I can share is that patents are expensive to maintain. So, before you do it, make sure you have a clear understanding as to why you want a patent for a thing. Fun story: the guy who invented the computer mouse, he patented that in 1970, well ahead of when people had computers in their house. That's an amazing world-changing invention that was patented where the inventor made basically no money on it because it was at the wrong time. He should have just kept that as a trade secret. And once home PC started proliferating, then he could put his patent in place.
I think it's important to figure out what's patentable, what should be a patent, and what should be a trade secret. I'm sure most creative engineers can just sit down and come up with a whole bunch of ideas that are novel and unique and patent them, but it's going to cost a lot of money and they may not go anywhere. So, think about what your purpose is before you go and apply for a patent.
And the timing, obviously.
DoneStreet
Yes, definitely, makes a lot of sense. Philosophically speaking, when you're 80 years old and looking back, what do you want to have accomplished in life
Andrew
Honestly, I'll be pretty happy, and I'll have no way of measuring this, if I've just created some positive impact, big or small, from all the people that I interacted with. That's what it's about at the end of the day.
DoneStreet
Yeah. Building positive relationships and uplifting others.
Andrew
Yeah. I'm hoping that I have produced some good products and technology in the world as well. But I think those are less important than the actual human interactions for sure.
DoneStreet
That's a pretty humble answer for such a driven, accomplished and intelligent guy.
Where can we send people to follow your work and updates?
Andrew
Yeah, I'm not a social media guy, so Formlabs.com would be the best place to send them. And even better, I am currently hiring every engineering function, so you could just come work with me. If you're a talented engineer or engineering manager, go to our website and put in your resume. Best way to follow what I'm up to.
DoneStreet
Great. And you're looking for hardware engineers, software engineers, firmware, everything?
Andrew
Everything, yes. Mechanical, electrical, optical, thermal, engineering managers - every function right now.
We hope you enjoyed this interview. If you would like to be featured in a future interview, please contact our team at innovationinsider@donestreet.com.
To learn more about DoneStreet and why our customers love us, follow this link.
Spend Less Time Hiring, More Time Building. Hire With Confidence Through DoneStreet.
If you have not yet subscribed, please hit the subscribe button and let us know what types of content you’d like to see more of in the future.
Thanks for reading Innovation Insider - Presented by DoneStreet! Subscribe for free to receive new posts and updates.